Listen to Tribonex’s pitch at TBB.2023
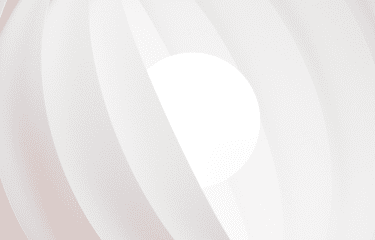
Energy efficiency
Cost-efficient and scalable surface treatments for minimised friction and wear in various industrial applications
Commercialised by
Tribonex AB
Uppsala, Sweden
Knivstagatan 12, 75323 Uppsala, Sweden
A patented mechano-chemical process creates durable low friction surfaces on components. The process is flexible and cost-efficient as it can be implemented using standard production machines, allowing for scalability and seamless integration in existing production lines. The process can replace current polishing steps, adding performance at low cost. The treatment can be applied on components made of steel or cast iron and of various shape and size, thus having very broad applicability.
The need
More than 20% of all energy used globally is lost due to friction and wear in various applications, including vehicle transmissions, bearings, pumps, compressors etc. Friction results in energy losses, while wear limits the lifespan of vehicles, machines and equipment which then need replacing.
The solution
A patented mechano-chemical process creates durable low friction surfaces on components. The process is flexible and cost-efficient as it can be implemented using standard production machines, allowing for scalability and seamless integration in existing production lines. The process can replace current polishing steps, adding performance at low cost. The treatment can be applied on components made of steel or cast iron and of various shape and size, thus having very broad applicability.
The value proposition
Listen to Tribonex’s pitch at TBB.2023